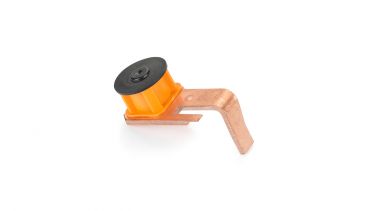
Enhance your application’s performance with Bus Bar prototyping
Creating the perfect bus bar: from engineering and prototyping to serial production.
Prototypes play a crucial role in the design and development process of a bus bar. They allow for visualization and validation of ideas before mass production, resulting in a more efficient and streamlined approach. At RPK Group, our engineers work closely with yours to design, test, and manufacture high-quality bus bars, from initial prototypes to full-scale production.
Benefits of developing, prototyping, and manufacturing bus bars with RPK Group:
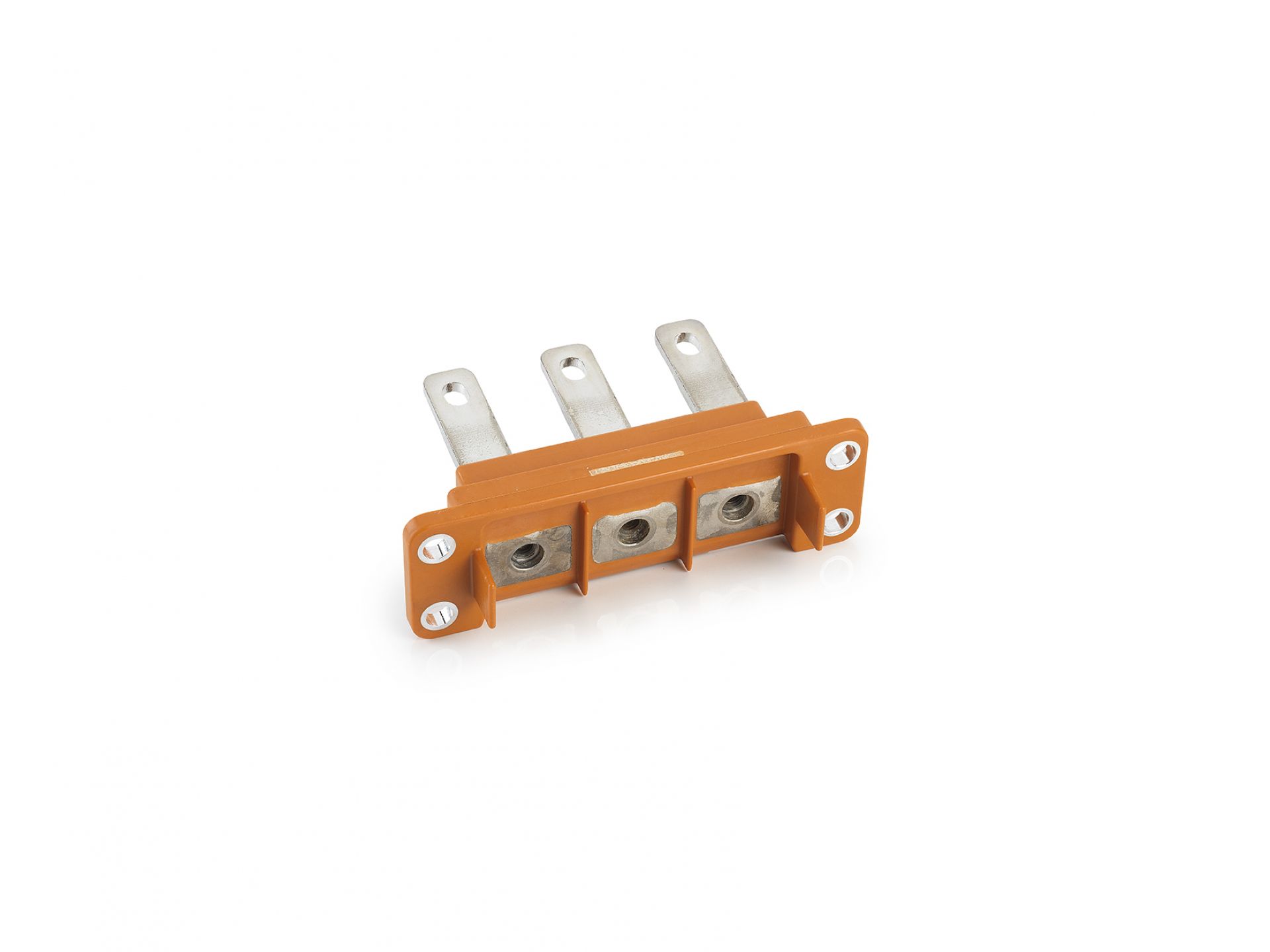
Validation of serial manufacturing technology through prototyping:
- Our expertise extends to various manufacturing techniques, including stamping, bending and CNC Multi-Slide forming, laser welding, insert placement, laser brazing pads, vibration, assembly, and coating
- Prototypes are a valuable testing ground for validating these manufacturing methods, ensuring a seamless transition to serial production
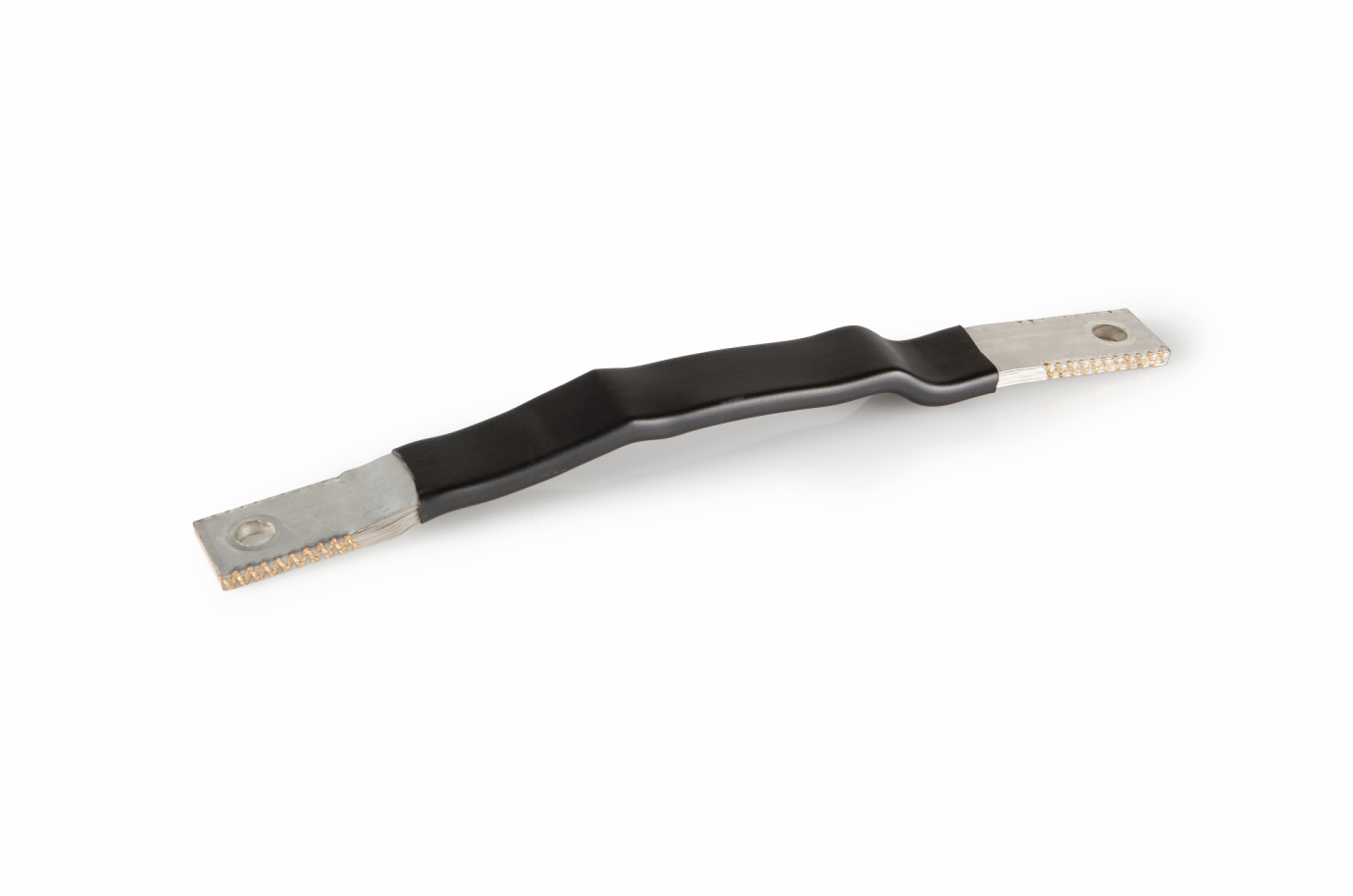
Dynamic time-to-market response:
- We maintain a quick-response mindset, making us an ideal partner for engineering development and seamless progression to mass production
- Our existing production capabilities are adapted for prototyping, allowing us to accelerate the time to market for your bus bar solutions
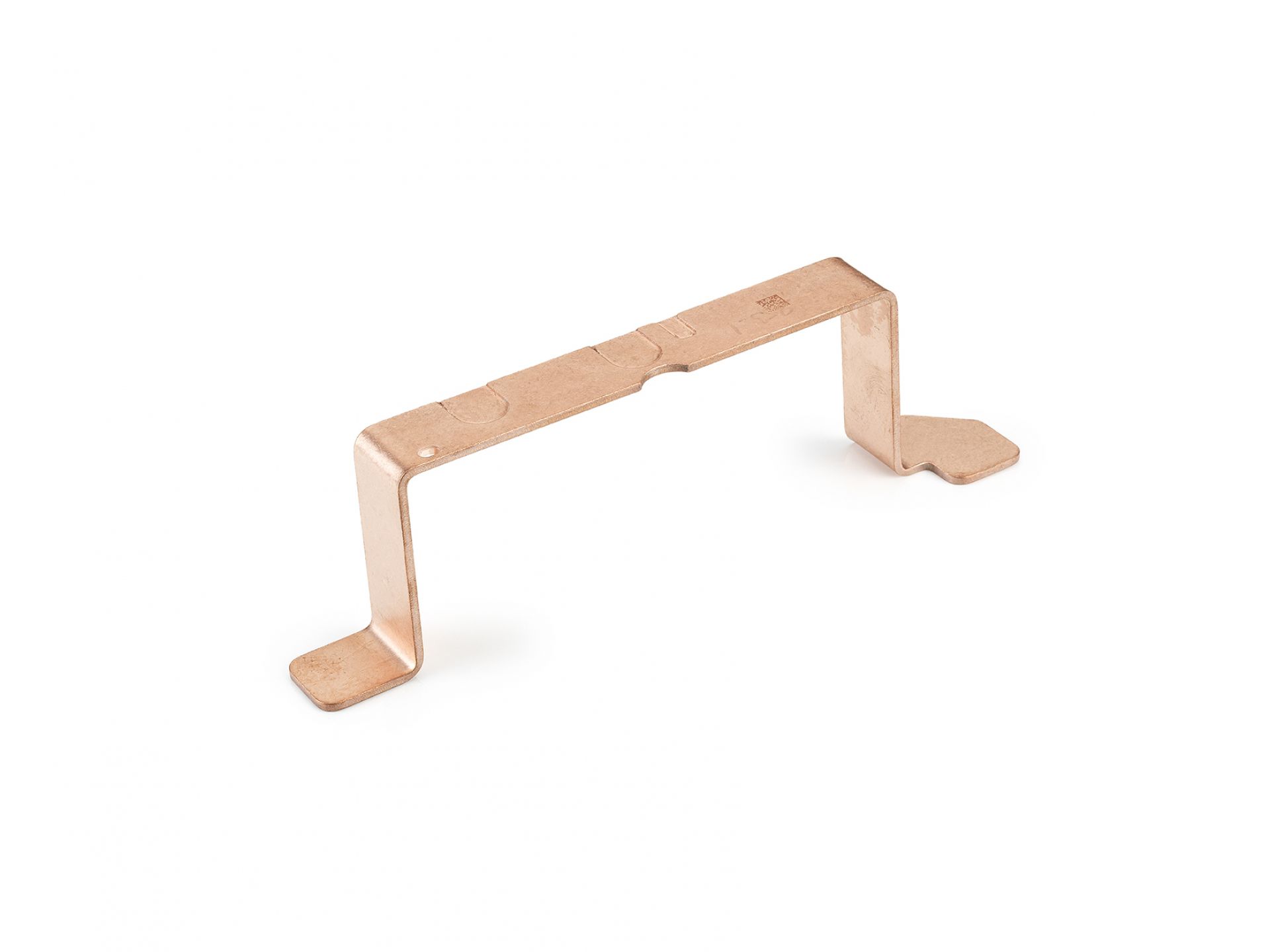
Technical validation with state-of-the-art measurement tools:
Our advanced measurement tools enable fine-tuning of designs even before full-scale production begins:
- 2D and 3D geometry measurement: precise measurements ensure optimal fit and performance
- Static and dynamic thermal testing: prototypes undergo rigorous thermal assessments
- Mechanical testing (push out and torque out): we evaluate mechanical strength and durability
- Electrical testing (insulation, conductivity, and Kelvin contact resistance): prototypes are thoroughly tested for electrical performance
- Comprehensive test reports accompany each piece, providing valuable insights for clients
Bus bar applications in hybrid and Electric Vehicles
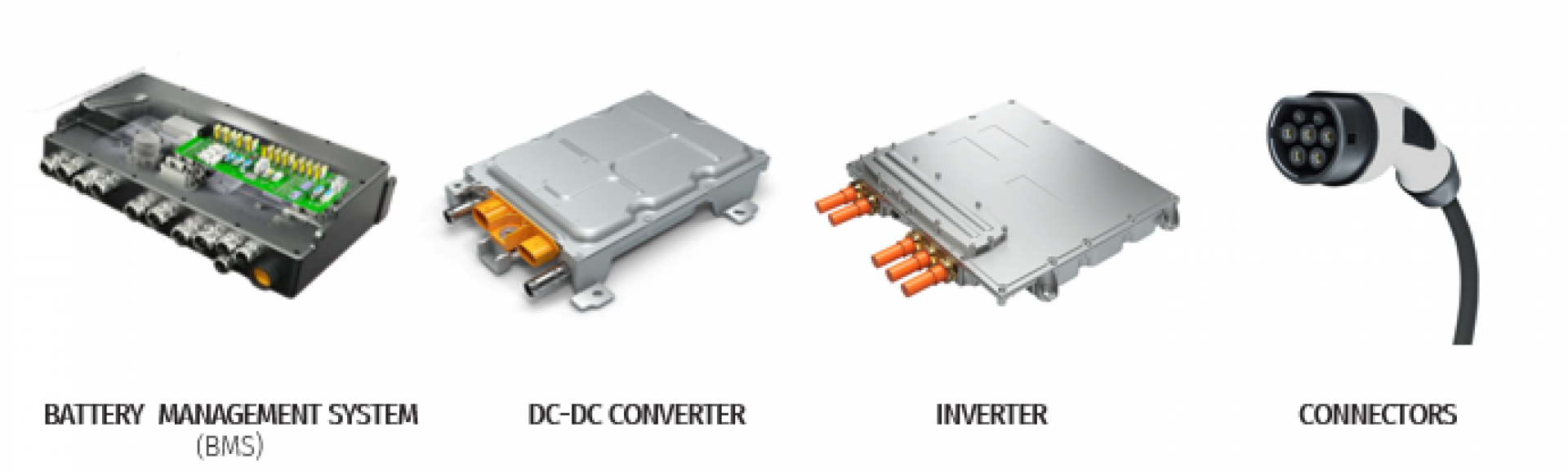