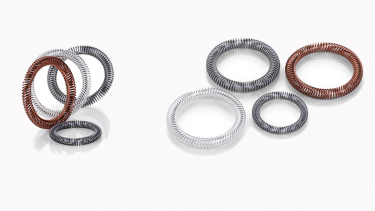
Case Study: Custom Canted/Slant Coil Springs, Precision Engineering Solutions
Combining helicoidal compression springs and welding expertise for optimal power management and mechanical retention.
By Mikel Ortigosa and Rubén Díaz
Thanks to the experience gained from working for different sectors and technologies, our engineers at the RPK Group technology center can develop customized solutions for our customers.
Challenge
In this case, the challenge was to combine knowledge of helicoidal compression springs with welding experience gained in e-mobility projects.
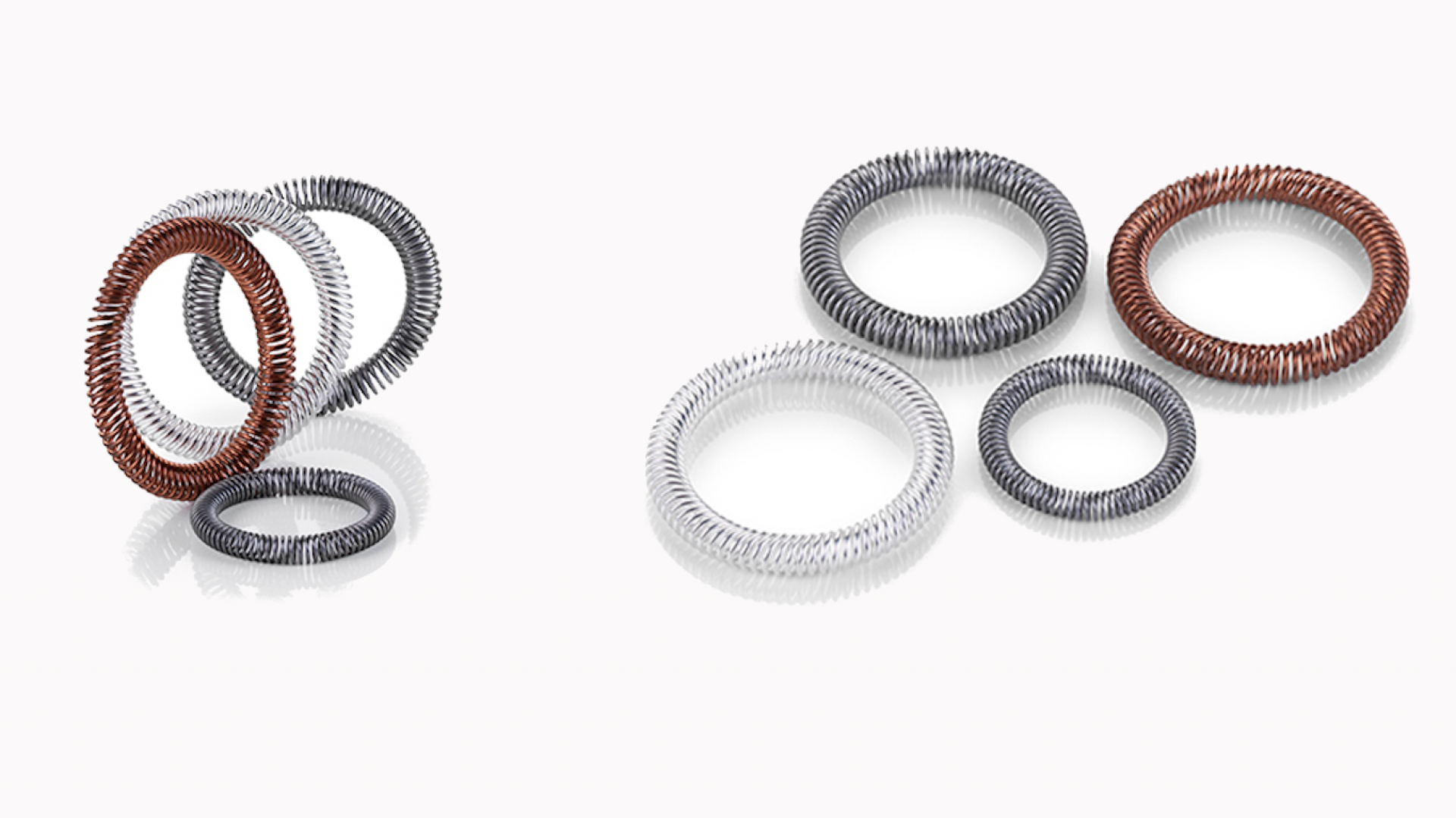
RPK Group's canted springs are utilized to effectively handle higher power within confined spaces while maintaining cooler operating temperatures. Our canted coil contact springs provide multiple contact points, delivering optimal conductivity and grounding for both static and dynamic electrical applications.
The design elements that affect the performance of canted coil springs include spring force, wire material, wire diameter, coil height, and plating thickness. Our engineering team meticulously crafts these springs to excel not only in power management but also in mechanical retention, thanks to their consistent force, and electromagnetic shielding (EMI).
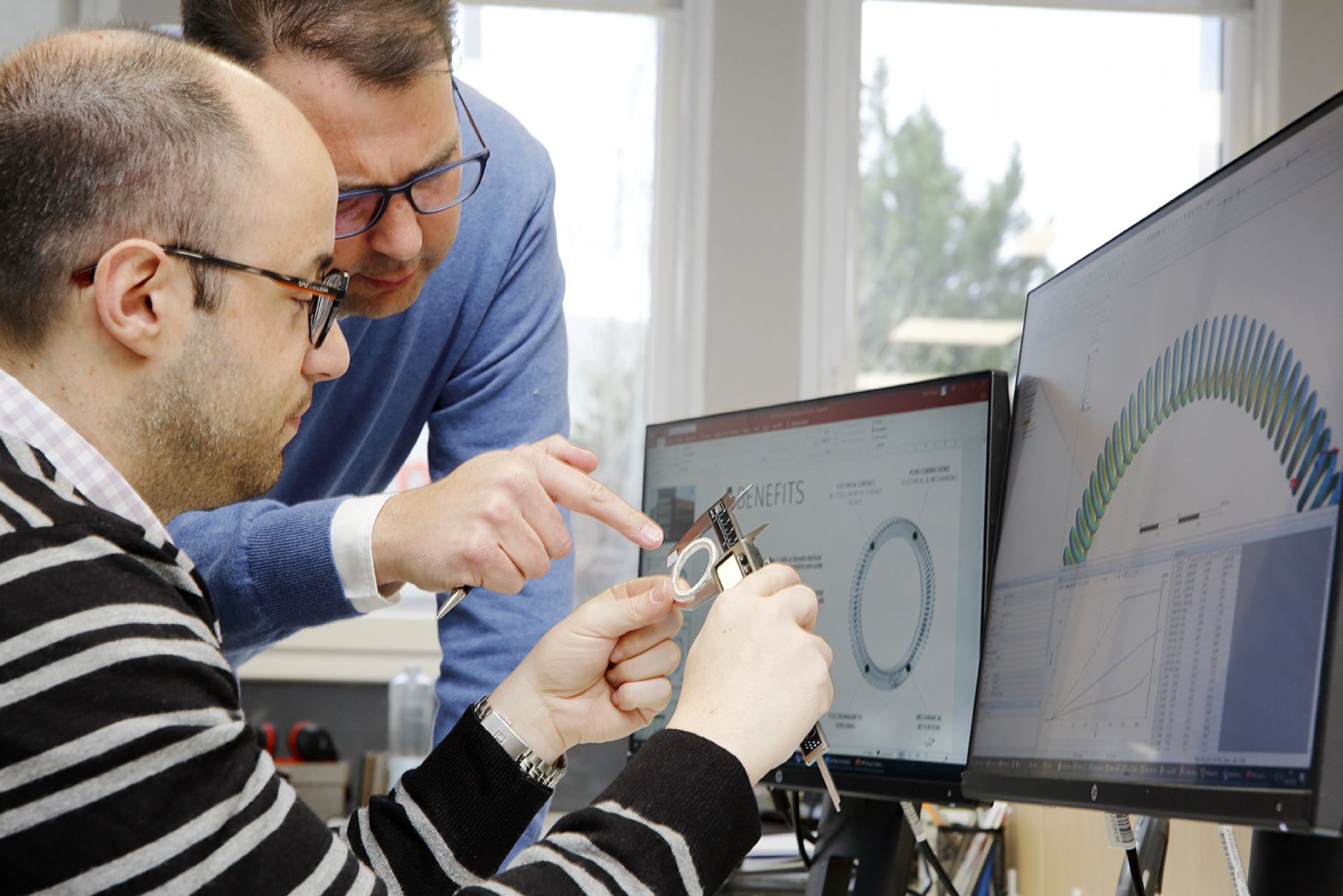
Development
RPK Group's client presented specific load and electrical requirements for a canted spring, prompting the engineering team at the technical center to embark on a comprehensive development process. Leveraging their expertise in materials science and precision engineering, the team meticulously designed and refined the manufacturing process, tooling, and optimal welding techniques tailored to meet the client's specifications. Through iterative testing and experimentation with various materials, the team diligently fine-tuned the production parameters until they achieved the exacting requirements set forth by the client.
The technological center's dedication to innovation and problem-solving was evident throughout the development journey, as they continuously iterated and optimized every aspect of the canted spring production process. From material selection to welding methods, each step was carefully calibrated to ensure optimal performance and reliability, ultimately culminating in a product that not only met but exceeded the client's expectations. Through their collaborative approach and relentless pursuit of excellence, RPK's technical center successfully delivered a bespoke solution that precisely matched the client's unique requirements for load-bearing capacity and electrical performance.
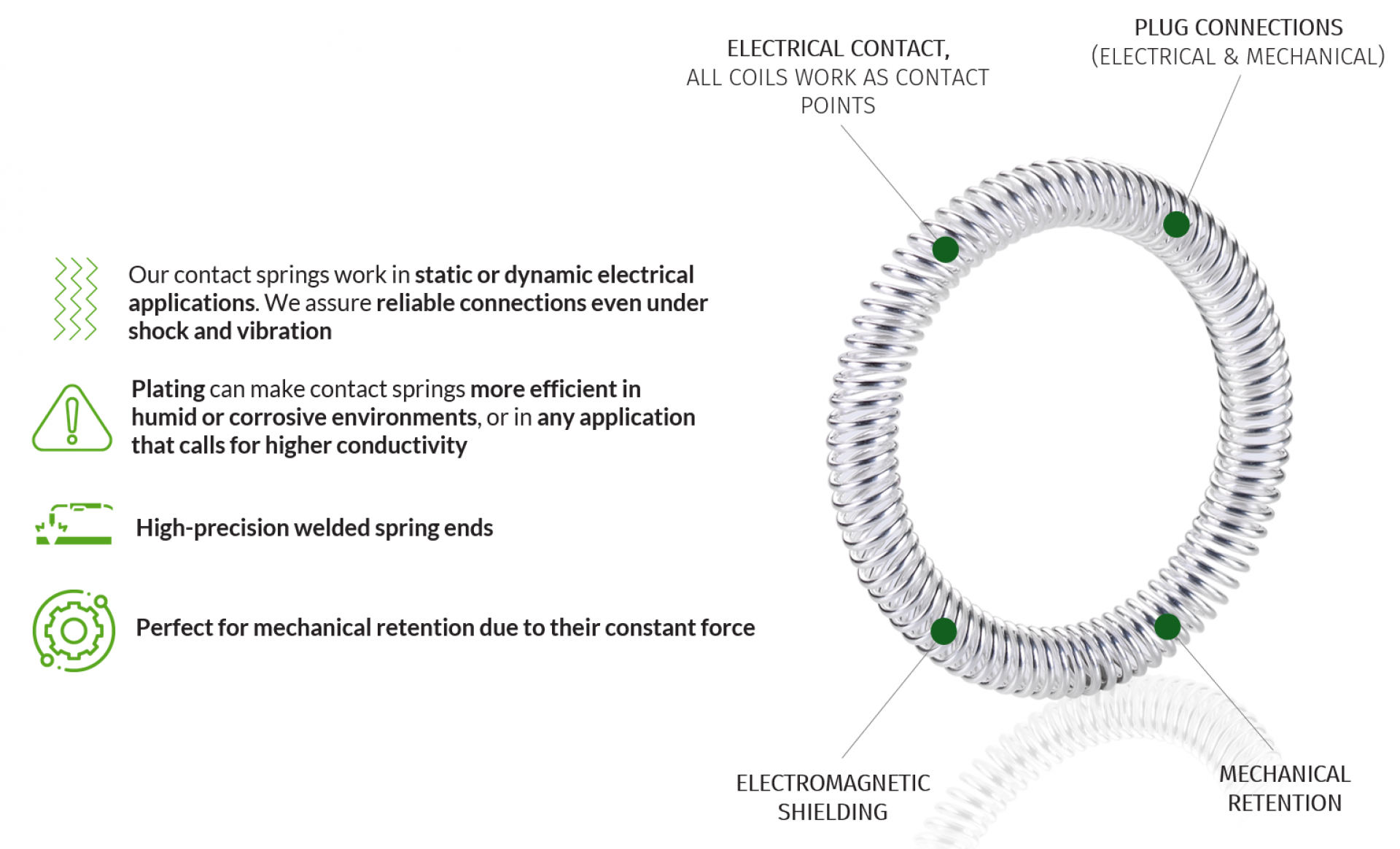