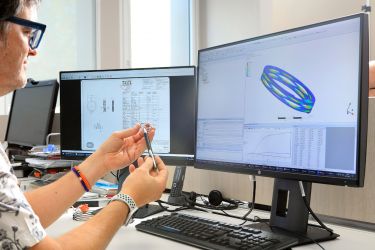
Case study: benefits of a Wave Spring vs Compression Coil Spring in a shock absorber valve
Why did we design a wave spring over a compression coil spring to solve issues due to limited space and lateral loads?
By Fernando González, product engineer at RPK Group, and Iñigo Fernández de la Peña, Engineer and Business Development Manager
RPK Group is a global leader in the engineering and custom manufacture of highly complex components, with a local presence in the main automotive, e-mobility, electric, industrial, and medical markets. As part of this leadership, RPK Group has been involved in the development of a shock absorber valve with a customer. The major constraints in this situation are the limited space in the assembly and the lateral loads of the compression spring, which can cause the valve to open unevenly. For that reason, the engineers are tending towards analyzing the idea of designing a wave spring instead of a compression coil spring.
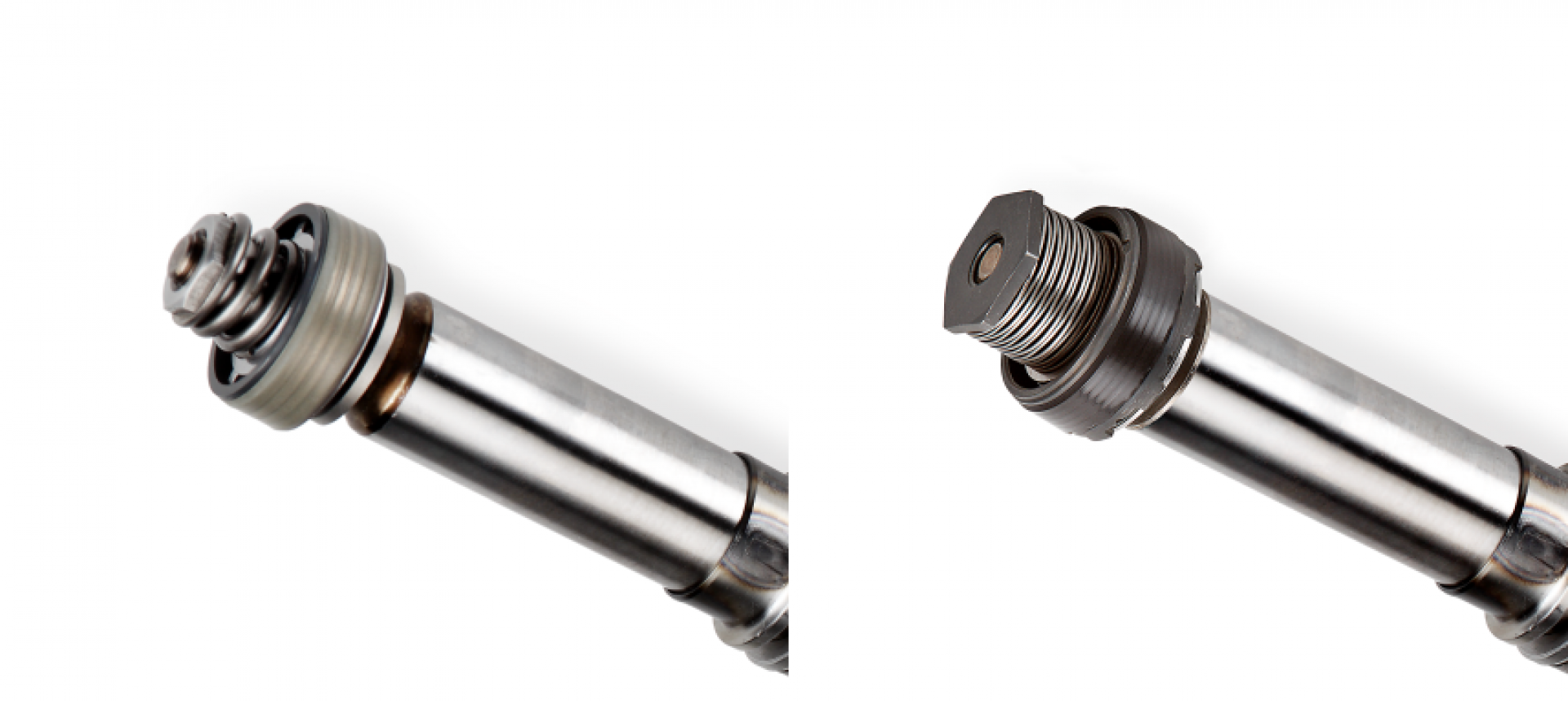
Main advantages of wave springs
- Axial space savings, possibly reducing 50% of the operating height
- Bending load in the waves guarantees 100% axial load transmission
- Low load tolerance at specified work heights
- More accurate spring rate and loads, with better tolerance, 50% tighter
- Creation of unlimited range of forces using wire size, wire form, no. of turns, turn configuration, no. of waves, and wave form
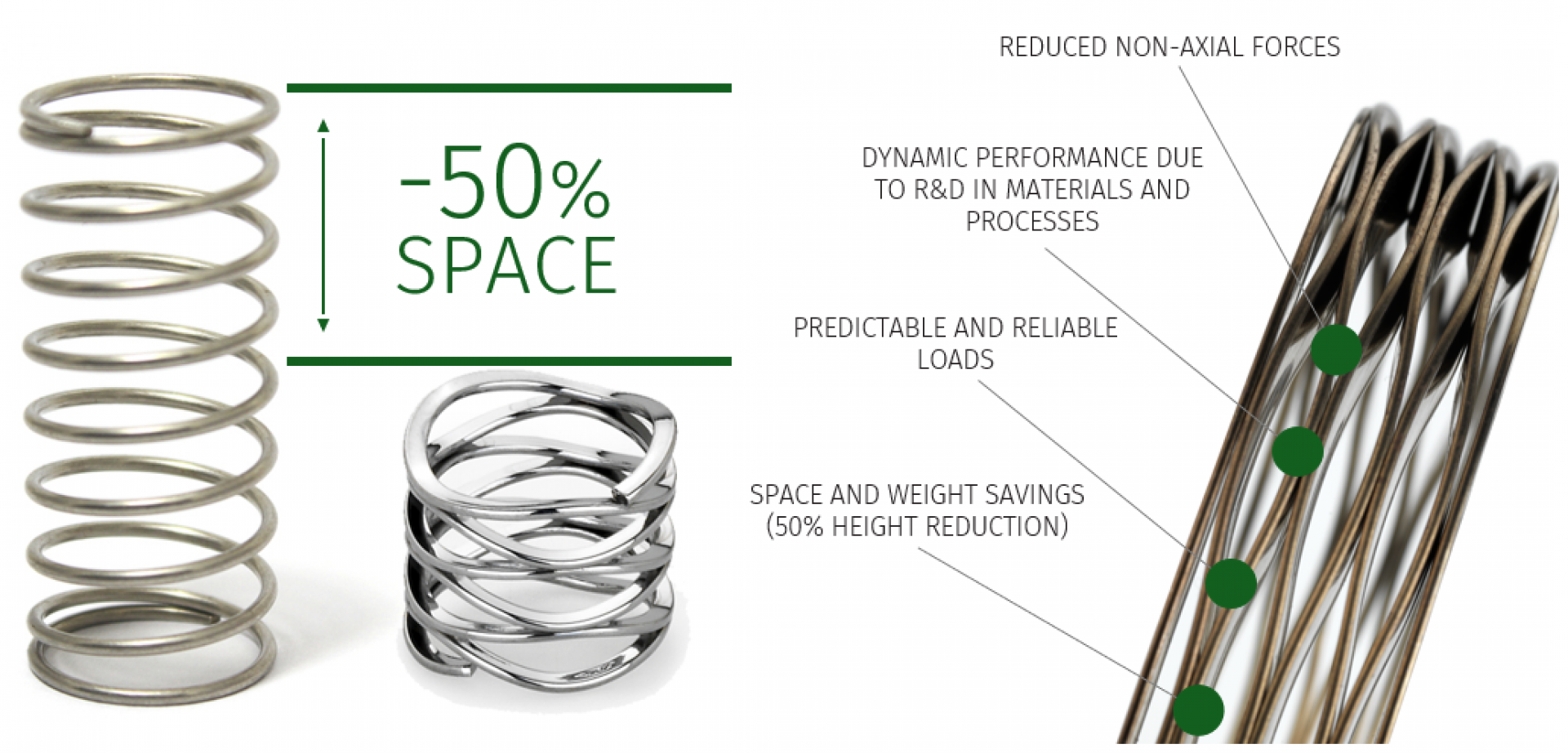
As a manufacturer of compression springs for 50 years and wave springs since 2005, RPK Group would like to share the results of our experience with both spring types using an empirical comparison of a real case.
Therefore, to sum up, these are the major advantages and disadvantages of this commonly used solution :
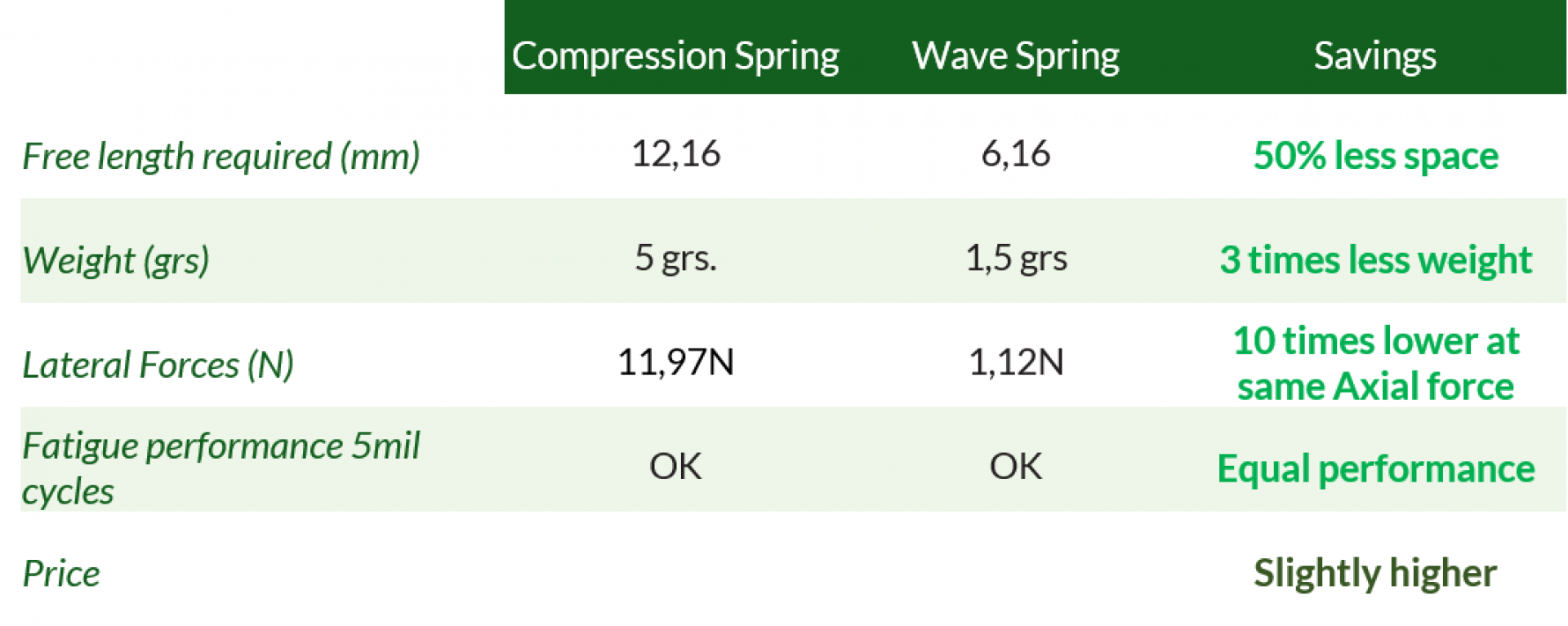